Rims make or break the car. An example is above.
As we all know, rims are the metal bits between your tire and the car. In that aspect, they are extremely important to how your car functions. Low quality rims can be warped (not round), poorly balanced (thus requiring a lot of weights to balance) or very weak (shatter on impact).
This would lead to vibrations in the steering wheel, loss of car control, an uncomfortable ride, bad fuel economy and can be possibly fatal – should the rim fail catastrophically.
Today, car rims are getting cheaper and cheaper. Imports from China have flooded the market, providing a great variety of sizes and patterns. BUT…… are all these rims good? Or does the adage “you pay for what you get” stand?
OVERVIEW
Rim quality (in order from worst to best): Gravity Casted rim < Low Pressure Casted rim < High Pressure Casted rim < Liquid Forged rim/Forged rim/Billet Machined rim
Most rims that are made in China are gravity casted, whereas some Taiwan rims are low pressure casted and one (to my knowledge) is liquid forged. Some Taiwanese rims are also roll forged. Japanese rims are minimally pressure casted and some are forged. European rims are minimally low pressure casted and some are forged. American rims sold in Singapore are generally forged.
One may be surprised that even big name brands such as Breyton manufacture their rims in China (albeit not all, some are still from Germany). Certain over-hyped brands use low tech manufacturing methods yet still sell at exorbitant prices (sorry guys, as much as I would like to identify what brands they are, this is a public document and I would refrain from being explicit due to litigation issues. However if you are really interested, do email us and I will give you a personal reply). It is kind of like paying a high premium for a BMW without getting the high performance of a BMW, if you get my analogy.
Autokinetics would like to share and discuss about this topic but first let us get down to the basics.
HOW RIMS ARE MADE:
Rims are manufactured in 6 different methods:
- Gravity casting
- Low pressure casting
- High pressure casting
- Roll forged
- Liquid forging
- Cold forging
*there are hybrid composition methods used by some Japanese companies such as SSR and Enkei but their basis technological concept is the same
1. GRAVITY CASTING
Gravity casting is the cheapest and the lousiest of methods to make a wheel. As its name suggests, gravity casting is basically pouring liquid alloy into a mould and using the force of gravity to allow the molten metal to conform to the shape of the wheel.
In this manufacturing process, all the metal entering the mould is subjected to turbulence. This turbulence can cause severe defects such as oxide inclusions and entrapped gas porosity and in certain cases, mould erosion and hotspots.
Why is gravity casting undesirable? Due to the wheels being susceptible to:
- Air cavities within the metal
- Uneven expansion during cooling
- Uneven material density
- Low density
- Poor surface finish
This leads to a wheel that is not only weak but imbalanced and heavier than equivalent designs of similar size. We purchased a 15” SSR Type F replica. Though it’s a 15” without the tyre, it required 30 grams of weight just to balance.
While it may not seem much that 35g of weight is placed along the rim, with tyres this weight was required to be increased to 70g, meaning that there is a large amount of inertia generated when the wheel is spinning at high speeds. Though it may seem minor, these weights have implications on braking, acceleration, stability and fuel consumption.
Gravity casted wheels are heavier as they require more metal in order to achieve the required strength for their purpose. Below we can see the material grain structure of a casted wheel.
Here we can see the porosity of a casted wheel. As we can see, the wheel snapped on impact due to the shearing forces acting along the grain. Simply said, the grain structure of gravity casted wheels is not ideal for rims. In the picture, it shows what happens to a casted wheel when things go terribly wrong. (Note: above rim should be low pressure casted)
A clear example of a gravity casted wheel: the finishing is so bad that you can see the porosity of the metal even after it has been painted. Note the bulges in the metal.
Beware, if you see this, don’t buy it. It’s a low quality wheel. No matter how cheap it is, you’re risking your life!
2. LOW PRESSURE CASTING
Low Pressure casting is an upgrade from Gravity casting; it is marginally more expansive to manufacture wheels using this method. The benefits of Low Pressure casting are that the metal has less air cavities and slightly better density uniformity.
Most (not all) casted car wheels manufactured in Japan and Europe use this technology. Due to the added cost, such technology is seldom seen among the cheap China-made options flooding the market these days. Certain rims from Taiwan also use this technology.
The full benefits of Low Pressure casting are:
- Less air cavities
- Decrease in unwanted exposure to air when the alloy is molten (changes its properties)
- Improved density distribution of the alloy
- Better tolerances due to more uniform contraction and expansion of alloy upon cooling
Low Pressure casting enables wheels to be stronger than Gravity casting. Alas, a casting is still a casting and the grain structure of the alloy is not ideal, resulting in fissures upon impact. Low Pressure casted wheels are still subjected to air cavities in the metal, thereby decreasing the strength of the wheel.
All in all, Low Pressure casted wheels are more desirable than Gravity casted wheels. They allow for low costs to manufacturers thus translating to low prices for consumers, while at the same time improving the quality and strength of the wheel.
Some wheel brands using Low Pressure casting are ADVANTI and Kyowa.
Below is a picture of the finish of a Low Pressure casted wheel:
Note the porosity of the metal, here it can be seen that the finishing is much better than that of a Gravity casted wheel.
3. HIGH PRESSURE CASTING
High Pressure casting is the best of all the casting methods. However it is more expensive to produce a wheel using this method. There are very few wheels that are manufactured using High Pressure casting.
The molten alloy is forced into the moulds thus increasing density, reducing air cavities and creating a wheel that is more precise. However the grain structure of the alloy is still that of a casted form. Hence although the material is much stronger due to how it is manufactured, the grain structure of the material is still has marginal porosity. As a result, compared to Forging and Billet Machining, High pressure casted wheels are still weaker and also heavier in order to be sufficiently strong for use, due to material density.
Nevertheless, High Pressure casted wheels are getting better with improvements in their strength and weight approaching to that of the quality of Forged wheels.
However they are undoubtedly expansive. A form of High Pressure casting can be seen in certain wheels brands such as ENKEI, SSR and BuddyClub. ENKEI is notable as they use a form of semi-solid high pressure casting which changes the grain structure of their wheels towards a forged wheel.
The benefits of High Pressure casting are the improvements over Low Pressure casting on all fronts:
- Denser material
- Reduced air cavities
- Tighter tolerances
- More concentric wheel as rims are less subjected to expansion and contraction irregularities upon cooling
This leads to a wheel that is stronger, lighter and has a better finish. Examples of High Pressure casted wheels are Team Dynamics Pro Race 1.2 18” at 9 kg (unconfirmed production method but confirmed weight).
4. ROLL/ROTARY FORGED
Roll Forged rims are a rare type of wheel though present in Singapore. Only certain shops carry it and they come mostly in big sizes i.e. 18 inch onwards.
Roll forged rims are basically casted rims that have specially treated barrel section. This means that the whole rim is casted and the barrel of the rim, which is in contact with the tyres are rolled, compressed and formed by another machine.
Therefore what we have then is a hybrid wheel. The centre of the wheel is casted (the spokes) and the rim/barrel of the wheel is high pressure rolled. What this gives is a wheel that is lighter than a casted rim and has a stronger rim/barrel section. It must be noted that these wheels are not truly forged, as its basis is a casted wheel.
Roll forged barrels have lines when stripped of its paint like this.
5. LIQUID FORGING
Liquid Forged rims are a new generation of rims utilizing a special method of manufacture. They are basically liquid metal forced into a mould and cooled under pressure, giving them the approximate grain structure of a forged rim. Although Liquid Forging and High Pressure casting seem similar, the amount of pressure used is very different. There is much more compressive force in liquid forging.
There are many benefits to liquid forging:
- Very precise components and tolerances
- Void of air bubbles just like a forged or billet rim
- Very even material density
- Good surface finishing due to minimal porosity
- Very light weight wheel due to high density of material achieved
A picture of the material porosity: it can be seen that there is next to no visible porous ‘holes’ (the black specks are paint spilled over from spraying)
Liquid Forged rims are as light and possibly as strong as forged rims but at a lower price. Their manufacturing process is much more expensive than any form of casted rim. However they are indeed the best bang for buck (value-for-money) wheels in the market; coming in at half to a third of the price of forged rims in Japan or Europe yet having all the structural benefits of its more expensive counterparts.
Liquid Forged rims are extremely rare, to our knowledge only one company used to produce them and they have since shut down the plant in Taiwan. (Please let us know if you know of any company that has this technology for rims, if you know of any, thanks)
This is as Liquid Forged wheels are not well known in the market and coupled with the low brand exposure have consigned the liquid forged wheel to oblivion… for now.
For those lucky enough to find these wheels, they used to be sold under the Magline brand in Singapore. Those who use it before would know how strong and true (round) these wheels are. I know, because I am using a Magline 8 which I purchased second hand to replace the initial wheels I had. My old set of casted wheels were not round when they were first sold to me brand new, they vibrated so badly that my metal watch would make a clacking sound on my wrist no matter how many weights I used to balance them.
What is even more appalling is that those wheels were from a very big tyre company… all I can say is that they were made in Philippines. To date after 8 years of driving, through Malaysia and bad roads and careless kerbing, the Magline rims are amazingly still perfectly round and have perfect balance. Best of all for a 16” wheel, it weighs in only at 5kg odd!
If you look closely you can see the damage to the rim on the bottom right corner, I used 280 grit then 400 grit sand papers to repair the damage.
Balance is still perfect!
[youtube http://www.youtube.com/watch?v=lzRWD-BK-Zo&w=425&h=349]
Currently Autokinetics has the last remaining production run of Liquid Forged Magline 5 rims in Singapore. Unfortunately they are very limited and are only in 18” form and PCD 5×114.3 for Japanese cars. Once this stock is exhausted, there will be no more as I have received confirmation from the factory that they have closed down permanently. Sets are very limited (less the 11 remaining!) and are moving fast, call 91853389 (Bryan) or email sales@autokinetics.sg for enquiries.
[youtube http://www.youtube.com/watch?v=dPOg23vp1qU&w=560&h=349]
6. COLD FORGING
Cold forged wheels are wheels that are crafted like a samurai sword without the heating of metal.
Cold forged wheels are extremely costly to produce. They are made from a solid block of alloy metal using large hydraulic presses. Typically an 18” cold forged wheel costs between $900-2000 per rim. For certain Porsche rims, the price exceeds 2000 SGD per rim.
Cold forged rims are exceptionally strong and light. They are the best money can buy.
The benefits to cold forging are:
- Very precise components and tolerances
- Void of air bubbles
- Very even material density
- Good surface finishing due to minimal porosity
- Very high material density
- Very light weight wheel due to high density of material achieved
Companies that produce forged rims are NEEZ, HRE, ADV.1, Prodrive, Rays Engineering and so forth. While they are the best wheels money can buy, they are painfully expensive and thus normally do not come in small sizes. A 15” forged SSR Spec C costs around 500 SGD per piece. If you can afford one, get one. They are the best, with cold forged wheels, nothing else comes close.
Conclusion:
Wheels are an important part of your vehicle, dollar for dollar they represent the best upgrade you can make while improving your car. On the aesthetic front, they improve the look of your car like no other mod. Secondly, by allowing the decrease in rotating inertia and un-sprung mass, they provide more usable power, shorter braking distances, a more comfortable ride and improved handling.
So forget your lightened pulley systems or fancy body kits for now, put your money where it matters and where it would make the biggest difference to your drive, lap times, comfort and your safety.
Why does un-sprung mass and rotational inertia affect handling and comfort? COMING next…. The basics of handling…
I hope this sharing has managed to enlighten our esteemed readers out there.
Bryan Wong
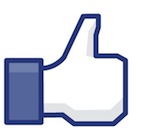
AutoKinetics – The Way it Should Be